From / SURBANA JURONG
By / EUGENE SEAH
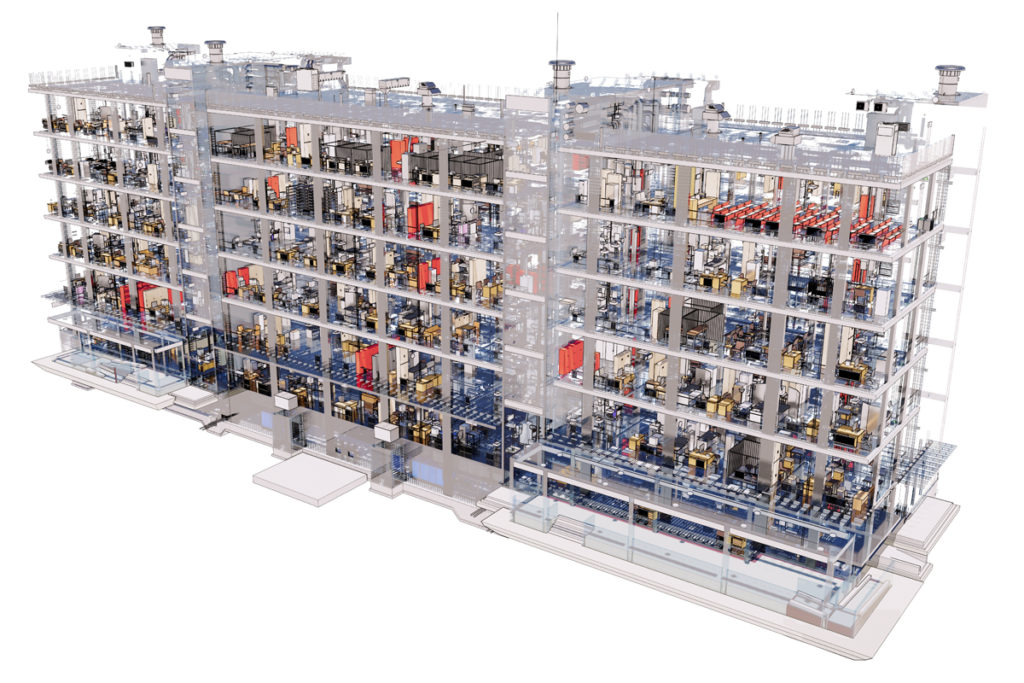
Transforming the construction sector to take advantage of the opportunities presented by digital technologies is a global challenge. Singapore has a vision to meet this challenge, but is the industry prepared for the scale of change required?
Introduction
The use of digital technologies is transforming the global construction industry. New data-led tools and processes are available with the capacity to boost productivity in design and construction and are already enabling new levels of efficiency and collaboration across the supply chain.
Singapore’s Building and Construction Authority (BCA) is embracing this opportunity and responding to other global challenges such as climate change and rapid urbanisation with its recently launched Construction Industry Transformation Map (ITM). This intends to power Singapore’s construction industry into the modern world by supporting supply chain skills to underpin competitiveness.
The widespread use of Integrated Digital Delivery (IDD), as illustrated in diagram 1, is one of three key initiatives driving the transformation announced by BCA on 24th October 2017. IDD sits alongside the adoption of Design for Manufacturing and Assembly (DfMA) techniques and the development of Green Buildings as key investments that the government hopes will radically change Singapore’s approach to construction.
Yet this transformation is a global challenge. As such, BCA’s ITM initiative looks to support existing home-grown design and management systems expertise and position Singapore’s industry ready to compete across other international economies. Changes to the syllabus taught in Institutes of Higher Learning (IHL), should see some 80,000 personnel trained to create a new national skill base ready to tackle these critical global challenges.
Diagram 1: Scope of Integrated Digital Delivery (IDD) – Credit source: Building and Construction Authority
Putting Integrated Digital Delivery at the Heart of Construction
Integrated Digital Delivery describes the use of digital technologies to integrate all processes and stakeholders throughout the construction lifecycle. It is a process which, using cloud-based technologies, enables a single, up-to-date source of project data to be accessed by all.
The adoption of Building Information Modelling (BIM) is the key to the success of IDD, enabling all parties and stakeholders to collaborate using advanced info-communications technology (ICT) and smart technologies.
However, there are also many design and dimensional uses of digital technologies and IDD encourages and enables information sharing while also reducing the risk of error and duplication. Technologies that underpin this delivery include:
- The use of Building Information Modelling (BIM) and all its different dimensions such as 4D time and scheduling, 5D cost management, 6D asset management and 7D simulations;
- Coupling peripheral technologies such as using drones for inspections;
- Virtual, mixed, immersive, and augmented reality for visualisation;
- Computational science to analyse data and optimise or even solve design challenges.
The BCA’s ITM puts these technologies at the heart of construction’s transformation to deliver more sustainable design and construction practices.
Making the Case for Digital Change
One of the biggest global challenges facing the construction sector as it prepares for digital transformation is overcoming the inherent social resistance to the use of new technologies. In such an established and conservative sector, establishing a robust plan for change is essential.
The move away from 2D design to embrace technology started with 3D Computer Aided Design (CAD). More recently, the widespread adoption of BIM has caused a major shift in thinking, practice, and process across the sector.
The shift towards the use of centralised cloud-based data storage as the foundation of Integrated Digital Design presents new challenges for a sector used to working locally. It will require industry professionals to adopt an open mind and to thoroughly question what and how processes should be changed to maximise potential gains.
Embracing this change should also include work to identify the potential gaps in knowledge or any immediate practical issues that might arise from the use of a cloud based system. Staff will need to be trained to embrace this new world.
Helping a generation accustomed to existing technologies and processes will require focus to steadily change their mind-set towards the use of new technologies and new ways of working. Awareness of the likely immediate impact on staff motivation is vital along with establishment of a change management programme designed to break down any barrier to adoption.
A New Approach to Design
The use of the powerful shared modelling, design and visualisation technologies are central benefits of Integrated Digital Design processes. They provide clients and developers with more options to interrogate and virtually “see” finished designs, and provide designers with an excellent opportunity to showcase and contrast a range of design options and considerations.
Significantly, this ability to rapidly assess multiple options across the design process, provides commercial opportunities. In effect, the firm capable of designing and demonstrating the best value solutions, with the best options and design, should be better positioned to win the job.
Diagram 2: Planned 4D-BIM vs Actual Progress (Project: Wisteria Mall, Mixed Use Development at Yishun Avenue 4, Singapore)
As a result, we also now see IDD, and in particular the use of 4D (as seen in Diagram 2 – the use of 4D BIM for design and consultancy works for Wisteria Mall in Yishun) and 5D BIM, driving a new approach to design in which construction and constructability is kept top of mind. This so-called Construction-Led-Design (CLD) boosts efficiency by integrating the design and construction process, preventing contractors from having to redesign proposals to suit their specific methods or working preferences.
Inevitably the sector will shift more and more towards this CLD approach as developers quickly realize that in a world of high land prices requiring quick product-to-market times, such techniques will improve yield, rates of return and profitability.
Embracing IDD processes should also underpin greater use of off-site fabrication and Design for Manufacturing and Assembly (DfMA – as seen in Diagram 3) principles to create a win-win across construction – from the client down through the supply chain. And from Singapore’s national economic perspective, this approach will improve productivity as measured by the Ministry of Trade and Industry (MTI).
Diagram 3: Design for Manufacturing and Assembly (DfMA) concept using Prefabricated Volumetric Construction (PPVC)
Unleashing the Power of Collaboration
Singapore’s ITM vision also called for greater collaboration across the construction supply chain, in the way that contracts are set out. The use of IDD is central to delivering this vision.
Traditional contracts can be adversarial, setting firms head to head with clear winners and losers. In contrast, collaborative contracts such as, for example, the New Engineering Contract, take a fairer approach; sharing information and working with a blameless culture.
The increased use of IDD in Singapore will inevitably accelerate the move towards more such collaborative contracts. But it will also prompt new roles in the industry, roles that help facilitate collaboration and help to avoid and/or decide on disputes faster so that the project can move on.
This change will require a new breed of professionals with facilitation and coaching skills to help foster better communication between the project team members. These individuals will not only have to be proficient in contracts, mediation and facilitation, but also have the technical skills to spot potential issues early.
The move to embrace digital technology will also change the way that construction professionals interact, with office spaces changing to accommodate tele-conferencing and virtual reality workshops. Co-location will be commonplace in construction teams and so-called WAR (Work Action Resolution) Rooms will enable geographically separated teams to collaborate and interact virtually.
Choosing the Right Hardware and Software
As the construction sector embraces the new digital world, it becomes increasingly important that professionals understand and manage the impact of their software and hardware choices and the associated costs.
The market for construction-focused hardware and software has grown rapidly. For example, in the virtual reality field, there are already a multitude of solutions available based around products such as the Microsoft HoloLens and HTC Vive headsets and many other platforms exist to create bespoke Immersive Virtual Reality Rooms. Each has its specific purpose, capital and operational cost, and maintenance regime which need to be thoroughly understood.
Similarly, there are also several types of collaborative platforms with different brands serving different purposes. Choosing the wrong software not only can be costly but may also cause users to dislike the software, taking them longer to embrace new work processes.
The Need for Education
Greater use of digital technology in construction has prompted a transformation in the way professionals are educated and a change to the subjects taught at universities and technical colleges.
Globally it is vital that industry works closely with academia to set out the requirements of a modern construction syllabus. With Singapore’s universities now adopting a mix of academic and practical learning, Institutes of Higher Learning (IHL) are increasingly seeking volunteers from industry to transfer their practical knowledge into education.
There is also an increasing trend for private and public-sector firms to create corporate laboratories in schools in which academics and practitioners sit together to resolve technical and management issues.
However, as more and more of engineering design becomes computerised and modelled, there are growing calls from industry for IHLs to focus on the basics and ensure that the foundations are taught well. Without these basic skills, the use of IDD process could propel the production of poor or even life-threatening designs.
Conclusion
The use of IDD will see future designs optimised, with buildings hosting a wide array of high-tech Internet-of-things (IoT) sensors and monitors to improve building performance, boost the quality of life for occupants and aid facilities management.
Yet embracing the required change will not be straightforward for many in this traditional sector. Leadership is vital to embed new technologies into process management and to encourage the adoption of new working practices and tools by staff.
To maximise the opportunities that this change presents, industry must shape the sector to capitalise on the digital journey. That means making investment not only in the vital hardware and software tools necessary to embrace a digital future, but also in the education required to provide professionals with the right skills.
However, it is also clear that for construction to embrace its digital future, educators cannot overlook the teaching of core engineering knowledge. While digital process can certainly enhance design and communication, there will still be a vital need for human participation, leadership and engineering skill.
This article is co-created by Surbana Jurong Academy.